Torque loss in bolts is a common issue in mechanical assembly, and it can directly affect the reliability and safety of the connection. The factors that cause torque loss in bolts mainly include the following aspects:
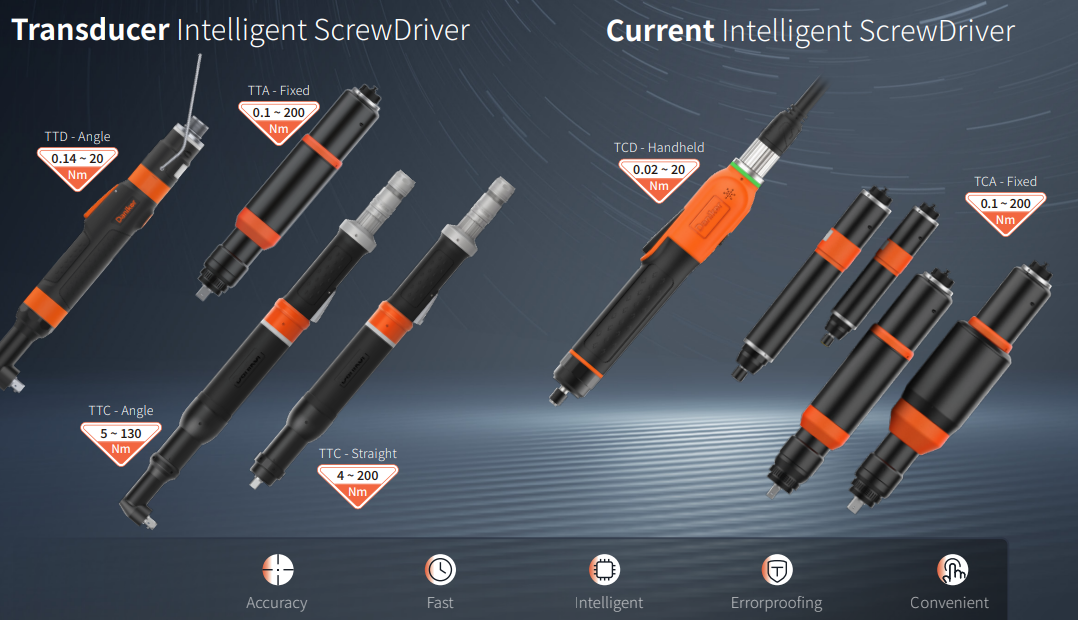
I. Surface Factors of Assemblies
The surface roughness of assemblies is a key factor. When bolts come into contact with assemblies, rough surfaces can cause uneven pressure distribution. This uneven pressure distribution can lead to stress concentration in some areas, while other areas may not achieve the required clamping force. Over time, these stress-concentrated areas are more prone to fatigue and relaxation, thereby accelerating torque loss.
II. Material Factors
For some soft connection materials, such as plastics and rubbers, their physical properties can lead to torque loss. These materials tend to exhibit creep when subjected to force. Creep refers to the gradual deformation of a material under long-term external force over time. This deformation can cause the clamping force of the bolts to gradually dissipate, thereby reducing torque. For example, in the assembly of some automotive components, if plastic connection parts are used, special attention needs to be paid to the issue of torque loss.
III. Tightening Process Factors
The tightening process also has a significant impact on torque loss. If the tightening speed is too fast, it can cause local stress concentration. When bolts are tightened quickly, the elastic deformation of the material cannot keep up with the tightening speed, which can easily lead to excessive stress in local areas. These stresses will gradually be released during subsequent use, resulting in torque loss. In addition, improper tightening sequence can also cause similar problems. If the tightening sequence is not reasonable, it can lead to some bolts being subjected to excessive stress, while other bolts have insufficient stress, thereby disrupting the overall stress balance and accelerating torque loss.
To reduce torque loss, the following measures can be taken:
I. Optimize Surface Quality of Assemblies
Before assembly, the surface of the assemblies should be treated appropriately to reduce surface roughness. This can be achieved through processes such as grinding and polishing to make the surface of the assemblies smoother and flatter. This allows for more even pressure distribution between the bolts and the assemblies, reducing stress concentration and thereby reducing the likelihood of torque loss.
II. Reasonably Select Materials and Design Structures
For cases involving soft connection materials, the creep characteristics of the materials should be fully considered. During the design phase, materials with better creep resistance can be selected, or the thickness of the connection parts can be increased, or the shape of the structure can be changed to enhance their creep resistance. At the same time, during the assembly process, the torque value should be set reasonably according to the characteristics of the material to avoid over-tightening.
III. Optimize Tightening Process
During the tightening process, the tightening speed should be controlled. The rotation speed should be appropriately reduced during the tightening phase to allow the elastic deformation of the material to better adapt to the tightening process. In addition, adopting a two-step or multi-step tightening strategy is very effective. For example, first perform a pre-tightening with a lower torque to release some stress, and then proceed with the final tightening. This can better release the residual stress generated during the tightening process and reduce torque loss.
In terms of tightening sequence, a diagonal tightening sequence can be used. For multi-bolt connections, diagonal tightening can ensure even stress distribution and avoid excessive local stress. In addition, for some large or complex assemblies, multi-axis synchronous tightening can be used. This method can tighten the bolts simultaneously with multiple tightening axes, further ensuring the uniformity of the tightening force and effectively reducing torque loss.
Using Danikor electric screwdrivers can help reduce torque loss to a certain extent. Danikor electric screwdrivers have accurate torque control functions and can set torque values according to different tightening requirements. Their advanced control systems can ensure the uniformity and stability of the tightening speed, avoiding torque loss caused by excessive speed. In addition, Danikor electric screwdrivers can also be used in conjunction with automated tightening equipment to achieve functions such as multi-axis synchronous tightening, further improving tightening quality and reducing the risk of torque loss.